Exciting news coming out of Far North Queensland for mi-Support – renovations are underway for…
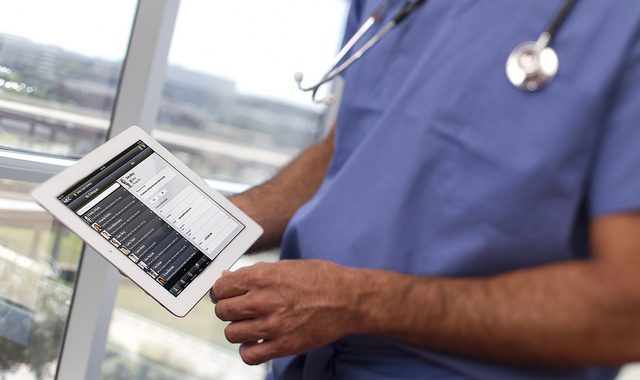
The value of process improvement in healthcare
Process improvement sounds like something that belongs on a factory floor– but it’s an approach that can benefit hospitals and healthcare organisations throughout the patient journey, and deliver savings of 30 per cent or more in some areas.
Having led a number of process improvement initiatives, the key is not to let yourself get daunted and to make a start; you can almost always identify some ‘low hanging fruit’ or easily-implementable efficiencies.
Process improvement starts with identifying and documenting your processes and procedures from admission to discharge with one question at the forefront of your mind: “Why?”
The project team can (and should) put a toddler to shame when it comes to the frequency of “Why?”… Why is the process necessary? Why is this step needed? Why should it be done by that person rather than this one? Why do this in-house?
Substantial efficiencies can result from process improvement. For example, an overhaul of transcriptions for independent medical examiners, MedHealth, resulted in a 40 per cent cost reduction – and an increase in quality, reliability and speed. On my estimates, most hospitals that perform transcriptions in-house could achieve savings of at approximately 20-40 per cent by adopting a similar solution.
Process improvement can occur in isolation in one area or as part of an external framework. The most common process improvement framework is ISO, in particular the ISO 9001 quality standard. ISO 9001 aligns well with existing regulation and can assist with compliance under other compulsory certification frameworks.
However, ISO shouldn’t be completed just for certification’s sake or as a marketing gimmick but as a real benchmark for future improvement and better business value – directly and indirectly facilitating better care for the patient.
Like any other change, ISO certification requires buy-in from the top, and the close involvement of operational staff who will need to use the new process when complete. When making changes, project teams also need to consider how staff can continue with ‘business as usual’; a staged approach is often easier to implement than a ‘big bang’.
As part of the ISO process, organisations would:
-Have periodic management reviews, using the same framework in different areas or sites;
-Increase management knowledge of, and control over, activities;
-Experience increased information flow through the organisation;
-Have a strong incentive to perform internal audits;
-Solicit customer feedback to prevent future problems; and
-Assess risk, again using a proven framework, including workplace health and safety.
If the hospital hierarchy is not willing to commit to a process such as ISO, managers can still use process improvement techniques within their areas of expertise.
With hospitals increasingly outsourcing services such as cleaning, food preparation and information technology, leading suppliers are also seeking ISO accreditation. According to one industry estimate, over 30 per cent of healthcare providers in Australia and New Zealand outsource one or more non-clinical support services.
For external companies seeking to partner with hospitals, ISO accreditation offers a degree of certainty on quality and improvement within their particular service, however, maximum benefits could be expected from an integrated approach across an entire healthcare organisation or chain of organisations.
Comments (0)